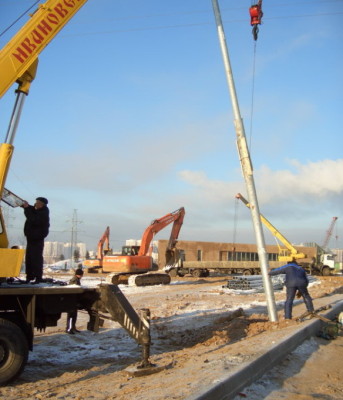
Prowizja akceptacyjna powinna zrzec się po zatwierdzeniu aktu komisji akceptacyjnej przez klienta. Od tego momentu obiekt zostaje przeniesiony na utrzymanie organizacji operacyjnej (klienta), która akceptuje jej saldo i rejestruje w określony sposób prawo własności do nowego obiektu w lokalnych organach wykonawczych.
Przed przystąpieniem do budowy napowietrznych linii energetycznych (OHL) należy wykonać następujące prace:
uzyskano zezwolenia na prace na trasie VL, w tym na obszarach lasów i gruntów rolnych;
tymczasowe pomieszczenia zostały przygotowane do umieszczenia zespołów instalacyjnych i stron pro-slave;
tymczasowe bazy do przechowywania materiałów są zorganizowane; sprawdził stan dróg, mostów i dróg dojazdowych do autostrady
VL, jeśli to konieczne, zbudował tymczasowe drogi dojazdowe; oczyścił pas ziemi wzdłuż autostrady, w okolicy lasu
polany są ułożone; Rozbiórka budynków przewidzianych w projekcie
znajduje się na linii napowietrznej lub w jej pobliżu i przeszkadza w pracy;
wykonano pikietę produkcyjną - instalacja wzdłuż linii napowietrznej pikiet, oznaczająca przyszłe miejsca instalacji podpór.
Po ułożeniu tymczasowych podstaw do przechowywania materiałów, materiały te są transportowane do obszaru, w którym znajduje się trasa OHL.
Transport podpór do autostrady VL odbywa się za pomocą specjalnych nośników macierzystych. Bębny z drutem są transportowane w pozycji pionowej, zabezpieczając je w tylnej części pojazdu za pomocą rozstępów z drutu stalowego. Izolatory z izolacją porcelanową i szklaną, wstępnie przetestowane i zmontowane w girlandach o wymaganej długości i przetransportowane na trasę VL w specjalnych drewnianych pojemnikach, które chronią izolatory przed uszkodzeniami mechanicznymi.
Rozładunek podpór i bębnów za pomocą drutu powinien odbywać się z reguły za pomocą dźwigów.
Dostawa sprzętu budowlanego na autostradę VL odbywa się za pomocą własnej mocy lub na specjalnych platformach samochodowych.
Montaż podpór. Stojaki drewnianych drążków (ryc. 2.1) połączone są w zakładkę z betonowymi konsolami (pasierbami). Konsole z drewnianym stojakiem są połączone za pomocą stalowych drutów lub bandaży stalowych jarzma. Do bandaży używa się miękkiego drutu ocynkowanego o średnicy 4 mm lub drutu bez ocynkowanego o średnicy 5 ... 6 mm. Zakłada się, że liczba zwojów klamry wynosi:
12 - o średnicy drutu 4 mm;
10 - o średnicy drutu 5 mm;
8 - o średnicy drutu 6 mm.
Drewniane podpory dla linii napowietrznych o napięciu 35 kV i więcej są dostarczane przez osobne elementy (stojaki, trawersy, stężenia), których montaż odbywa się za pomocą połączeń śrubowych.
W stojakach drewnianych słupów napowietrznych o napięciu do 10 kV wiercone są otwory do przykręcania stalowych haków, na których izolatory sworzniowe są wzmocnione zaślepkami z polietylenu. Na trawersach drewnianych wsporników VL w kształcie litery U o napięciu 35 kV i wyższym elementy otworów łączących są montowane w wywierconych otworach w celu dalszego mocowania łańcuchów izolatorów. W razie potrzeby na stelażu drewnianego wspornika kładzie się uziemiające zejście z drutu stalowego.
Włączone słupki betonoweah VL za pomocą specjalnych zacisków są zamontowane na trawersie stalowej. W przypadku linii napowietrznych o napięciu do 10 kV, poprzeczki te mają sworznie, na których izolatory sworzniowe są wzmocnione zaślepkami z polietylenu. W przypadku linii napowietrznych o napięciu 35 kV i powyżej na końcach poprzecznych ramion instalowane są elementy złączek do dalszego mocowania łańcuchów izolatorów napowietrznych.
Metalowe wsporniki są dostarczane przez oddzielne elementy, których montaż między nimi odbywa się za pomocą połączeń śrubowych. Po zakończeniu montażu wsporników metalowych ich powłoka antykorozyjna zostaje przywrócona w miejscach jej uszkodzenia podczas transportu i montażu.
Montaż podpór odbywa się jak najbliżej miejsca przyszłej instalacji. Podczas montażu używanych dźwigów, podnośników i innych mechanizmów i narzędzi. Zmontowane wsporniki muszą być zgodne z rysunkami roboczymi projektu OHL.
Podstawy podpór. Metalowe wsporniki są instalowane na fundamentach żelbetowych (fundamentach) lub paliach. Rowy na fundamenty metalowych słupów opracowywane są przez koparki. Zbrojenie słupów żelbetowych w gruncie odbywa się poprzez uderzenie wibroizolacyjne
w pewnym sensie. Głębokość fundamentów lub pali musi być zgodna z projektem OHL.
Ryc. 2.1. Drewniane (a), żelbetowe (b) i stalowe (c) podpory VL:
1 - podpórka stoiska; 2 - mocowanie żelbetowe (pasierb); 3 - bandaż z drutu stalowego lub stalowego kołnierza; 4 - haki do wzmocnienia izolatorów; 5 - usztywnienie dla sztywności; 6 - trawers; 7 - złączki do mocowania sznurków izolacyjnych; 8 - fundamenty żelbetowe.
Równolegle z instalacją fundamentów instalowane są urządzenia uziemiające - instalowane są sztuczne pionowe i poziome uziemniki. Żelbetowe fundamenty podpór są używane jako naturalne przewody uziemiające.
Górne części fundamentów żelbetowych są poziomo wypoziomowane i na nich jest zamontowany sztywny szablon, odpowiadający wymiarom dolnej części metalowego wspornika. Następnie doły są wypełniane warstwowym ubijaniem gleby. Szablon jest usuwany po zasypaniu dołów.
Żelbetowe i drewniane podpory są instalowane bez fundamentów. Studnie do drewnianych i żelbetowych wsporników są opracowywane przez specjalne wiertarki. Średnica wykopu powinna przekraczać dolną średnicę (rozmiar) kolumny wsporczej o 5 ... 10 cm Głębokość wgłębień powinna odpowiadać projektowi OHL.
Montaż podpór. Metody montażu wsporników zależą od ich konstrukcji, fundamentów, a także od dostępności różnych środków i mechanizmów podnoszących. Większość obsługuje się za pomocą
dźwig o odpowiedniej ładowności. Odjazd i ruch roboczy wysięgnika żurawia powinny zapewniać pełne podnoszenie podparcia, przesuwanie go do miejsca instalacji i utrzymywanie go w pozycji pionowej, aż wspornik zostanie zamocowany na fundamencie lub w ziemi.
Podczas instalacji podpory jest sprawdzana jej pozycja pionowa. W przypadku metalowych podpór stosuje się uszczelki metalowe, które są instalowane pomiędzy piątym wspornikiem a górną płaszczyzną fundamentu z betonu zbrojonego. Pionowość słupów drewnianych i żelbetowych uzyskuje się dzięki tymczasowym opóźnieniom i zatrzymaniom aż do ostatecznego zamocowania w ziemi. Doły pod drewnianymi i żelbetowymi podporami po wyrównaniu ich pozycji pionowej są wypełnione mieszanką żwirowo-piaskową z ubijaniem warstw po warstwie.
Instalacja przewodów (kabli) przeprowadzana jest osobno na każdym odcinku OHL ograniczonym przez dwie najbliższe podpory kotwiące (rozpiętość kotwicy) i składa się z następujących podstawowych operacji:
ekspansja drutów, w tym ich połączeń i wzrostu na podporach; napięcie drutu z regulowanym ugięciem; mocowanie przewodów do wsporników izolatorów.
Przed zwijaniem drutów do podpór, zawieszane są specjalne rolki montażowe (2.2, a), na których drut jest zawieszany w procesie walcowania, a następnie wykonywane jest kolejne naprężenie drutu.
Rozciąganie drutu odbywa się za pomocą mechanizmu trakcyjnego (ciągnika) i można go przeprowadzić na dwa sposoby:
instalowanie bębna z przewodem na urządzeniu stacjonarnym (kozły lub podnośniki śrubowe) na początku odcinka przeznaczonego do montażu i zabezpieczającego koniec drutu na ciągniku poruszającym się po drodze
(Ryc. 2.2, b);
ustalenie końca drutu na początku odcinka przeznaczonego do zamontowania i zainstalowania bębna za pomocą drutu na ciągniku poruszającym się po torze.
Drugi sposób zwijania zapewnia lepsze zabezpieczenie drutu przed uszkodzeniem mechanicznym z powodu tarcia na podłożu, jednak zastosowanie tej metody jest ograniczone. W szczególności niemożliwe jest rozwinięcie się i wysunięcie środkowego drutu na drewnianych podporach w kształcie litery U z ukośnymi prętami.
Ryc. 2.2. Rolka montażowa (a) i fragment walcówki (b);
a): 1 - dysk; 2 - składany policzek do układania drutu; 3 - zawieszenie do montażu, b): 1 - podpora kotwiczna; 2, 3 - pośrednie podpory; 4 - bęben z drutem; 5 - drut; 6 - mechanizm trakcyjny (ciągnik); 7 - wałek montażowy.
Ta technologia walcowania jest stosowana do gołych (nieizolowanych) drutów aluminiowych i stalowo-aluminiowych.
Obecnie izolowane przewody są szeroko stosowane w liniach energetycznych o napięciu do 20 kV. Dla napięcia do 1 kV stosowane są samonośne izolowane przewody (CIP), które są izolowanymi przewodami skręconymi w wiązkę. Osiowy przewód przenoszący obciążenie (przewodzący) może być wykonany bez izolacji lub z izolacją. W niektórych projektach CIP wszystkie przewody są przenoszone przez nośniki. Linie z SIP są oznaczone jako VLI.
Dla napięć powyżej 1 kV stosowane są przewody z przewodem jednoprzewodowym (ZIP). Linie z takimi przewodami są oznaczone jako VLZ.
Izolowane przewody w porównaniu z nieizolowanymi mają wiele zalet, między którymi można wyróżnić większą niezawodność i niższe koszty operacyjne.
Główną cechą toczenia izolowany drut należy zachować szczególną ostrożność podczas montażu, aby zapobiec uszkodzeniu powłoki izolacyjnej.
Na rys. 2.3 jest schematem walcowania izolowanych drutów w rozpiętości kotwy. Przy jednej podpórce kotwowej na rozrzutniku zainstalowany jest bęben z izolowanym drutem. To urządzenie do rozwijania musi być wyposażone w hamulec. Przy innym wsporniku kotwiącym, mechanizm rozwijania jest mocowany za pomocą elektromechanicznego wciągarki i wiodącego kabla o odpowiedniej długości.
Walcowanie izolowanego drutu odbywa się w dwóch etapach. W pierwszym etapie lider kablowy zostaje rozwinięty z rozwijania
mechanizm do bębna za pomocą drutu. Wciągarka mechanizmu rozwijania jest podłączona do rozwijania liny prowadzącej. Toczenie odbywa się za pomocą dowolnego mechanizmu trakcyjnego. Równocześnie z zwijaniem kabla jest on podnoszony na podporach i układany w rolkach odwijania, którego tarcza jest wykonana z tworzywa sztucznego lub metalu z powłoką z tworzywa sztucznego.
Po przewróceniu linki prowadzącej jego wolny koniec jest połączony za pomocą taśmy montażowej z końcem izolowanego drutu przy bębnie. Pończochy montażowe nakłada się na drut i zabezpiecza bandażem o długości co najmniej 0,5 m.
Ryc. 2.3. Proces zwijania izolowanych przewodów:1, 2 - wsporniki kotwiące; 3, 4, 5 - podpory pośrednie; 6 - bęben z izolowanym drutem; 7 - mechanizm rolkowy z wyciągarką; 8-żyłowy kabel; 9 - izolowany drut; 10 - skrzyżowanie kabla i drutu; 11 - wałek montażowy
W drugim etapie wykonywane jest zwijanie izolowanego drutu. Dla tego mechanizmu wciągarki raskatochnogo jest zawarty na uzwojenia lidera kabla. Walcowanie drutu należy przeprowadzić poprzez dokręcenie, z powodu siły nacisku wciągarki i urządzenia hamulcowego na bębnie za pomocą drutu. Napięcie jest konieczne, aby wyeliminować możliwość zwisu drutu do ziemi i uszkodzenia jego izolacji przed tarciem na ziemi.
Aby zapobiec pętlom w CIP podczas zwijania, należy zainstalować krętlik pomiędzy obsadą montażową a linią prowadzącą.
Podczas rozwijania przewodów nawiązywano połączenie. Odsłonięte druty aluminiowe i stalowo-aluminiowe o przekroju do 185 mm2 są łączone za pomocą owalnych łączników, które są aluminiową rurką o owalnym przekroju. Końce połączonych przewodów są wkładane do złącza z różnych stron, po czym łącznik jest skręcony za pomocą przenośnych narzędzi montażowych (rys. 2.4, a) lub obciskanych (Rys. 2.4, b).
Ryc. 2.4. Połączenia przewodów aluminiowych i aluminiowo-stalowych
Aby zwiększyć niezawodność połączenia stykowego i zmniejszyć jego opór przejściowy, krótkie końce przewodów, które mają zostać połączone, wychodzące z owalnego złącza, są spawane za pomocą wkładu termitowego (rys. 2.4, d).
Druty stalowo-aluminiowe o przekroju 240 mm2 i więcej łączone są za pomocą złączek kompresyjnych składających się z dwóch rurek - stalowych i aluminiowych (ryc. 2.4, c). Do łączenia takich przewodów używana jest przenośna prasa ręczna. Za pomocą stalowej rury 1, końce stalowych rdzeni połączonych drutów są ściskane razem, a aluminiowe części połączonych drutów są ściskane razem za pomocą aluminiowej rury 2 umieszczonej na wierzchu stalowych drutów.
W jednym przęśle linii napowietrznej nie można przyłączyć więcej niż jednego połączenia na przewód każdej fazy.
Do łączenia izolowanych przewodów przykręcone,
zaciski wytłaczane lub automatyczne (zaciskowe). Te ostatnie są bardzo wygodne do zainstalowania, ponieważ końce połączonych drutów po włożeniu ich do zacisku automatycznie klinują się w zacisku, zapewniając wymaganą wytrzymałość uszczelki.
Ryc. 2.5. Samonośne, izolowane połączenie przewodów
Połączenie CIP pokazano na rys. 2.5. Połączenie nieizolowanego przewodu neutralnego wykonano za pomocą zacisku 2 zaciskowego, połączenie drutów fazowych jest zaciśnięte. Uwolnione od izolacji końców połączonych przewodów fazowych
wkładany do rękawa 1, przykryty warstwą izolacji od zewnątrz i prasowany razem za pomocą prasy ręcznej. W procesie zaciskania powstaje niezawodny kontakt elektryczny i uszczelnienie przez tuleję tulejową. Aby zapobiec rozwijaniu się CIP, paski mocujące 3 są zainstalowane po prawej i lewej stronie połączenia.
Napięcie drutu(Rys. 2.6, a) jest wykonywany za pomocą mechanizmu trakcyjnego (ciągnik, wciągarka). Podczas napinania przewodów należy monitorować przejście przez rolki instalacyjne miejsc, w których występują połączenia przewodów, a sygnalizatory powinny być ustawione na przecinających się drogach.
Ryc. 2.6. Napięcie drutu (a) i harmonogram instalacji (b)
Gdy druty są naprężone, reguluje się ich odchylenie zwisu f - odległość między linią prostą łączącą punkty zawieszenia drutu na podporach i najniższym punktem obwiązywania drutu. Regulację ugięcia przeprowadza się zgodnie z harmonogramem instalacji (rys. 2.6, b), zgodnie z faktyczną temperaturą powietrza, rodzajem drutu i długością przęsła.
Pomiar zwisających drutów można wykonać na różne sposoby. W szczególności do tych celów wykorzystuje się najprostsze urządzenie - wysokościomierz kieszonkowy (ryc. 2.7). To urządzenie jest płaskim pudełkiem 1, mającym kształt trapezu równobocznego, w górnej części którego znajdują się otwory kontrolne 2, a szkło jest wkładane do podstawy, na którą nakłada się dwa rodzaje ryzyka - górny 3 i dolny 4.
Aby określić wysokość mierzonego obiektu H, obserwator odsuwa się od niego, trzymając urządzenie z otworami widokowymi w pobliżu oczu, w odległości L, przy której górne ryzyko pokrywa się z wierzchołkiem obiektu, a dolne z jego podstawą. Geometryczne wymiary urządzenia i ryzyko na szkle są wykonane tak, że H = L / 2. Pomiar odległości L nie stanowi problemu.
Ryc. 2.7. Pomiar wysokości obiektu
Aby określić zwisanie drutu, najpierw zmierzyć wysokość zawieszenia drutu na podporze, a następnie odległość od najniższego punktu luzu drutu do podłoża i znaleźć różnicę między uzyskanymi wartościami. Błąd pomiaru takiego urządzenia wynosi 3 ... 4%, co jest całkiem do przyjęcia.
Zamontuj nieosłonięte przewody wsporniki kotwiąceah Napięcie VL do 1
kV z izolatorami kołkowymi jest wykonywany poprzez skręcenie przewodów za pomocą tak zwanej "wtyczki" (rys. 2.8, a). W wieżach VL o napięciu powyżej 1 kV z izolatorami prętowymi, przewody mocuje się za pomocą pętli uformowanej za pomocą zacisku śrubowego (rys. 2.8 b).
Ryc. 2.8. Mocowanie przewodów na wspornikach kotwowych z izolatorami kołkowymi (a, b); z izolatorami wiszącymi (w)
Mocowanie drutów na wspornikach kotwowych z izolatorami podwieszanymi odbywa się za pomocą zacisków (rys. 2.8, c). Zacisk 1s
za pomocą łączników 2 mocuje się go do dolnego izolatora girlandy 3. Drut w zacisku dokręca się za pomocą zacisków za pomocą śrub typu U4.
Na podporach kotwowych krótkie końce drutów (pętle), pochodzące z dwóch zacisków w tej samej fazie, są połączone za pomocą zacisków śrubowych lub przyspawane za pomocą wkładu termitowego.
Ryc. 2.9. Mocowanie CIP na wsporniku kotwicy:1- wsparcie; 2 - opóźnienie; 3 - hak; 4 - zacisk kotwiący; 5 - z zerowym rdzeniem; 6 - przewody fazowe; 7 - zacisk
Ryc. 2.10. Montaż części zapasowych na wsporniku kotwicy: 1 - wsparcie; 2 - opóźnienie; 3 -
przemierzać; 4 - izolator zawieszenia; 5 - zacisk zaciskowy; 6 - izolowany drut; 7
- złączki do mocowania izolatorów na trawersie; 8 - złączki do mocowania zacisku naprężającego do izolatora.
Mocowanie izolowanych drutów na wspornikach kotwiących Linie napowietrzne o napięciu do 1 kV wykonywane są bez izolatorów (rys. 2.9) za pomocą zacisków kotwowych mocujących przewód zerowy nośny.
Mocowanie izolowanych drutów na wspornikach kotwicznych VL o napięciu powyżej 1 kV odbywa się za pomocą izolatorów podwieszanych i zacisków śrubowych z naprężeniem (ryc. 2.10). Korpus zacisku i płyta dociskowa wykonane są ze stopu aluminium. Moment dokręcania śrub zaciskowych jest ustandaryzowany i zaopatrzony w klucz dynamometryczny. Wielkość momentu jest podana na korpusie zacisku lub w specyfikacji.
Zamontuj nieosłonięte przewody podpory pośrednieah z izolatorami prętowymi z lepkich drutów aluminiowych (ryc. 2.11, a). Na wspornikach pośrednich z podwieszanymi izolatorami drut z rolek montażowych jest przenoszony na zacisk podtrzymujący 1 (Rys. 2.11, b) przymocowany do dolnej części izolatora 2. Drut w zacisku jest dokręcony za pomocą zacisków przy pomocy U kształcie spinki do włosów 3. Na rys. 2.11, b pokazuje polimerowy izolator zawieszenia.
Ryc. 2.11. Przewody mocujące na wspornikach pośrednich z izolatorami kołkowymi (a) i izolatorami zawieszenia (b)
Mocowanie izolowanych drutów na wspornikach pośrednich Linie napowietrzne o napięciu do 1 kV są wykonywane przez ułożenie zerowego rdzenia izolowanego drutu samonośnego w podtrzymującym zacisku śrubowym (ryc. 2.12). Mocowanie części zamiennych na wspornikach pośrednich linii napowietrznych o napięciu powyżej 1 kV za pomocą izolatorów kołkowych odbywa się za pomocą lepkiego przewodu do izolatora (ryc. 2.13).
Oddziały z linii z CIP(Rys. 2.14, a) są wykonywane za pomocą przykręcanych zacisków przebijających (Rys. 2.14, b) bez usuwania izolacji z drutu. Po zamontowaniu gałęzie na klipsach są zainstalowane
pokrowce ochronne wykonane z odpornych na warunki atmosferyczne i promieniowanie UV tworzyw sztucznych.
Ryc. 2.12. Mocowanie CIP na pośrednim wsporniku: 1- wsparcie; 2 - hak; 3 -
podpierający zacisk śrubowy; 4 - z zerowym rdzeniem; 5 - przewody fazowe
Ryc. 2.13. Montaż części zapasowych na wsporniku pośrednim:1 - wsparcie; 2 - trawers; 3-kołkowy izolator; 4 - drut; 5 - przywiązanie przewodu do izolatora
Ryc. 2.14. Oddział CIP (a) i zacisk do przekłuwania śruby (b):
1 - główna linia z CIP; 2 - oddział; 3 - zacisk przebijający w osłonie ochronnej
Instalacja przewodu uziemiającego podobne do okablowania.
Łączenie kabli odbywa się z reguły za pomocą stalowych złącz kompresyjnych. W liniach napowietrznych o napięciu do 110 kV mocowanie kabla do podpór odbywa się za pomocą złączek bez izolacji. Na linii napowietrznej 220 kV kabel jest przymocowany do wszystkich wsporników za pomocą izolatora zawieszenia, zwykle szkła, bocznikowanego iskiernikiem. W każdej sekcji kotwicy na jednej z podpór kotwowych kabel jest uziemiony.
Większość prac przy instalacji przewodów i kabli związanych z podnoszeniem wznoszeń. Na liniach napowietrznych o napięciu do 10 kV instalatorzy wspinają się na wsporniki, z reguły za pomocą mocujących pazurów i pasów. Na liniach wysokiego napięcia szeroko stosowane są wieże teleskopowe i podnośniki hydrauliczne.
Po zakończeniu wszystkich prac instalacyjnych na wieżach VL umieszcza się następujące znaki na wysokości 2 ... 3 m:
numery seryjne podpór; Numer VL lub jego symbol;
znaki informacyjne o szerokości strefa ochronna; plakaty ostrzegawcze na wszystkich nośnikach w populacji
teren
2.4. Instalacja rurowych urządzeń rozładowczych i urządzeń uziemiających
Wyładowanie rurowenoski są przymocowane z zamkniętym końcem do elementów nośnych pod kątem 15 ° do poziomu z dolnym położeniem otwartego końca. Zamknięty koniec ogranicznika jest połączony ze zejściem uziemiającym na podporze wykonanej z drewna lub z metalowym przewodzącym wspornikiem (stal i żelbet). Długość iskiernika zewnętrznego jest ustawiona zgodnie z projektem OHL.
Ponieważ wyładowaniu iskiernika towarzyszy silne wydmuchiwanie gazu wytwarzanego przez łuk elektryczny, otwarty koniec iskiernika powinien być ustawiony w taki sposób, aby gazy spalinowe nie powodowały stropów międzyfazowych lub podłogowych. Strefy spalinowe ograniczników różnych faz nie powinny przecinać się i pokrywać elementy konstrukcji i przewodów linii napowietrznych.
Podczas instalowania linii napowietrznych o napięciu do 1 kV urządzenia uziemiającedo ponownego uziemienia przewodu neutralnego (przewód PEN), ochrony przed przepięciami, uziemienia urządzeń elektrycznych zainstalowanych na liniach napowietrznych. Powtórne uziemienia wykonywane są na końcach podpór linii i podpór z odgałęzieniami na wejściach do budynków, w których można skoncentrować dużą liczbę osób (szkoły) lub które reprezentują dużą wartość materialną (magazyny). Zabezpieczenia uziemienia przed przepięciami są łączone z wielokrotnym uziemieniem.
Schemat wykonania uziemienia zespolonego na drewnianym napięciu VL do 1 kV z samonośnymi izolowanymi przewodami pokazano na rys. 2.15. Przebieg uziemiający 1 wykonany jest z drutu stalowego o średnicy co najmniej 6 mm i jest przymocowany do korpusu nośnego za pomocą wsporników w kształcie litery U. Połączenie zejścia uziemiającego z przewodem neutralnym 2 wykonuje się za pomocą zacisku śrubowego 3. W przypadku wsporników z betonu zbrojonego drut neutralny jest połączony ze stalowym wzmocnieniem, dla metalowych wsporników - z korpusem nośnym.
Podczas montażu linii wysokiego napięcia o napięciu wyższym niż 1 kV, urządzenia uziemiające są instalowane na podporach:
z przewodem uziemiającym; z rurkowymi wyładowarkami, odłącznikami, bezpiecznikami i
inny sprzęt; żelbet i metal o napięciu 6 ... 35 kV.
Zjazdy naziemne na drewnianych słupach wykonane są z drutu stalowego o przekroju co najmniej 35 mm2 lub z drutu stalowego o średnicy co najmniej 10 mm.
W jakości uziemienia na liniach napowietrznych wszystkich napięć należy najpierw zastosować uziemienie naturalne (fundamenty żelbetowe). Przy niewystarczającej rezystancji uziemienia naturalnego instalowane jest sztuczne uziemienie 6 (ryc.
Strona 74 z 83
W budowie VL pracochłonne prace są ziemne: kopanie dołów do instalowania w nich betonowych lub drewnianych słupów, kopanie dołów na fundamenty i podnóżki na metalowe słupy. Podczas wykonywania prac na urządzeniu dołów prowadzone są wskazówki (patrz § 13.3). Aby obniżyć koszty czasu pracy tych prac, w wywierconych studzienkach instaluje się żelbetowe i drewniane podpory jednofilarowe. Wiertarki typu MRK kopalnia doły o średnicy 750, głębokości 4000 mm; Typ BM - o średnicy 800, głębokości 3000 mm i średnicy 650, głębokości 8000 mm; typ BMTP - o średnicy 650, głębokość 3000 mm.
Wytaczarki BM i MRK przeznaczone są do wykonywania odwiertów w glebach kategorii I - IV oraz BMTP - w glebach do VII kategorii (oprócz przenośnika ślimakowego do urządzenia dołączona jest wiertło rolkowe).
Wytaczarka BM-802-C (średnica wykopu to 650, głębokość to 8000 mm) może być wykorzystywana nie tylko do wiercenia w fundamentach, ale także do wiercenia studni na palach i układania pali w wiecznej zmarzlinie. Przy konstruowaniu napowietrznej linii przesyłowej do 20 kV, lżejsze wiertarki i maszyny dźwigowe typu BKM są zwykle używane do wiercenia otworów o średnicy 350, 400, 500 mm, 2000 i 2500 mm w glebach kategorii I-IV i do montażu w studzienkach podpór. Maszyny zapewniają możliwość wiercenia otworów i sezonowego zamrażania na głębokość 1 m.
Do kopania rowów prostokątnych na prefabrykowanych i monolitycznych fundamentach żelbetowych używane koparki jedno-kubełkowe na gąsienicach
U-652, który może być używany jako dźwig do załadunku i rozładunku podczas montażu podpór. Pojemność łyżki tej koparki wynosi 0,65 m 3, maksymalna głębokość kopania wynosi 5560 mm.
Kopanie prostokątnych rowów koparką w zamarzniętej ziemi jest możliwe tylko przy głębokości zamarzania do 0,25 m. Przy większej głębokości wykopów do pracy z koparką konieczne jest poluzowanie gleby lub wycięcie szczelin w ziemi. Organizacje Ministerstwa Energii do tego celu wykorzystują specjalne wiertarki typu BGM. Maszyna przecina zamarzniętą lukę gruntową. Następnie, za pomocą ciągnika, dźwigu i zawiesi, układ zamarzniętej gleby zostaje oddzielony od rozmrożonej gleby i usunięty ze studzienki. Miejsce wykopów jest wykopywane za pomocą koparki E-652 z koparką.
Stosy (żelbetowe i drewniane) są również wykorzystywane jako podstawy do metalowych i drewnianych podpór. Pale są zanurzone w ziemi za pomocą agregatu za pomocą metody wibracyjnego ciśnienia. Agregaty kruszyw wibracyjnych typu UHF na ciągniku T-100 zapewniają wgłębienie pali żelbetowych o przekroju 300X300 mm i długości 6 m, a na ciągniku T-140 - wgłębienie pali o przekroju 400X X400 mm i długości 7 m.
W zamarzniętym gruncie wiertnice są wiercone za pomocą wiertarki BM-802S, głowicy wiertarskiej specjalnego przeznaczenia lub poprzez wiercenie otworu za pomocą trzech specjalnych wiertarek. W zamarzniętej i kamienistej glebie czasami trzeba robić dołki za pomocą piaskowania. Za pomocą eksplozji wykopy są wykopywane na zwykłych glebach metodą wybuchowej konsolidacji gleby. Równocześnie z zanurzeniem stosu, jeśli to konieczne, zanurz i elektrodę uziemiającą, która jest przymocowana do stosu.
Instalacja fundamentów zgodnie z powyższym. Tolerancje dla montażu prefabrykowanych fundamentów żelbetowych dla wolnostojących podpór i podpór z dyszlem pociągowym muszą być zgodne z instrukcjami.
Podczas montażu i instalacji podpór należy przestrzegać technologii podanej w §13.3 powyżej oraz następujących wymagań.
Wielkość obszaru do montażu i instalacji wsparcia należy przyjąć zgodnie z mapą technologiczną lub schematem montażu wsparcia określonego w przestoju. Linie kablowe do wsporników muszą mieć powłokę odporną na korozję. Muszą one być wyprodukowane i oznaczone przed transportem podpór na tor i dostarczone na pikiety wraz z podporami. Montaż podpór na fundamentach, które nie są ukończone przez konstrukcję i nie są całkowicie pokryte ziemią, jest zabronione. Przed montażem podpór metodą obracania zawiasów należy zapewnić ochronę fundamentów przed siłami ścinającymi. W przeciwnym kierunku wynurzania należy użyć urządzenia hamującego. Nakrętki, podpora mocująca, muszą być owinięte do pełnego stopnia i zabezpieczone przed samoodkręceniem śrubą zakryvaniem na głębokość co najmniej 3 mm. Na nakrętkach fundamentów narożnych, wspornikach przejściowych, końcowych i specjalnych należy zainstalować dwie nakrętki i wsporniki pośrednie - jedną nakrętkę na śrubę Podczas montażu wspornika na fundamencie można zainstalować nie więcej niż cztery stalowe uszczelki o łącznej grubości 40 mm między piątym wspornikiem a górną płaszczyzną fundamentu. Wymiary geometryczne uszczelek w planie muszą być co najmniej wielkości pięty podpory. Uszczelki powinny być ze sobą połączone, a piąta podpora przez spawanie. Przed instalacją konstrukcji żelbetowych docierających do pikiety, należy ponownie sprawdzić brak pęknięć, ubytków, dziur i innych wad na powierzchni podpór, a także obecność hydroizolacji wykonanej przez producenta na powierzchni konstrukcji żelbetowych przeznaczonych do montażu w agresywnym środowisku. W przypadku częściowego uszkodzenia hydroizolacji fabrycznej powłoka musi zostać przywrócona na drodze poprzez pomalowanie uszkodzonych obszarów stopionym bitumem (klasa 4) w dwóch warstwach. Niezawodność mocowania w glebie wsporników zainstalowanych w wywierconych lub otwartych wykopach zapewnia obserwacja głębokości osadzania podpór dostarczonych wraz z projektem, śrub, płyt kotwiących i ostrożnego zagęszczania zatok wypełniania warstwami.
Dostarczone na szosie przygotowane lub zmontowane w miejscach zbiórki na autostradzie, podpory instaluje się bezpośrednio w dołach lub na fundamentach za pomocą maszyn wiertniczych i dźwigowych lub specjalnych mechanizmów - instalatorów dźwigów wsporników typu KVL-8 (rys. 13 19, a). Drewniane i żelbetowe podpory jednokolumnowe o ciężarze do 3-4 ton mogą być instalowane w wykopach za pomocą dźwigu samochodowego (ryc.13.19,6). W celu zwiększenia wysokości podnoszenia haka maszyny wiertniczej BM-104 w zaufaniu Energostroymontazh, zastosowano teleskopowy przedłużacz hydrauliczny, który jest instalowany zamiast górnej rury maszyny (rys. 13 20).
Ryc. 13 19 Montaż podpór
W systemie Ministerstwa Energii do instalacji słupów żelbetowych z cylindrycznym stojakiem o długości 22,6 m lub stożkowych słupów żelbetowych o długości do 26 m, stosowane były powszechnie suwnice KLEP-7 i KJBL-8 o nośności 7 i 8 ton. Na bazie tych maszyn instalator dźwigów KBL-12 o udźwigu 12 ton został zaprojektowany do montażu żelbetowych podpór o długości stojaka 26 metrów.
W chwili obecnej do podnoszenia i montażu w wykopach wierconych maszyną MRK-750 stosuje się jednokolumnowe żelbetowe podpory o długości 22 i 26 m, o wadze do 8 ton, zmodernizowany instalator dźwigów KBЛ-8M. Czas montażu pojedynczego wsparcia 26,4 m długości i wadze 7,47 ton w wywierconym otworze wynosi 35 minut (bez uwzględnienia czasu potrzebnego do przeniesienia dźwigu z pikiety do pikiety).
Ryc. 13.20. Teleskopowe przedłużenie hydrauliczne w celu zwiększenia wysokości haka dźwigowego:
1 - dolny link; 2 - środkowe ogniwo, 3 - górne ogniwo, 4 - kabel teleskopowy, 5 - siłownik hydrauliczny
Haki i poprzeczki z izolatorami są mocowane na słupach żelbetowych z jednym słupkiem i w kształcie litery A przed ich montażem. Żelbetowe i drewniane wsporniki słupów pojedynczych bez belek poprzecznych są instalowane w wykopie, wywiercone w ziemi, a zatoki są wypełnione. Podpory jednosłupkowe z górnymi śrubami są instalowane w wykopie bez śrub, a po napełnieniu studzienki głębokością 2/3 odrywają wykop, w którym dźwigy układane są za pomocą dźwigu. Śruby są przymocowane do wspornika za pomocą zacisków ocynkowanych, a następnie zapewniają końcowe zasypanie wykopu. Podpory z dwoma śrubami - górną i dolną - są instalowane w wykopach wykopanych przez koparkę. Obsługa instalacji wykonywana za pomocą dźwigu i ciągnika.
Montaż ciężkich i skomplikowanych podpór montowanych na ziemi odbywa się za pomocą belki montażowej ("opadającej") poprzez obrót zawiasów przymocowanych do wspornika i fundamentu.
Montaż podpór w obszarach górskich, bardzo trudnych i podmokłych realizowany jest za pomocą śmigłowców.
Pozycja podniesionych podpór przed sprawdzeniem zamocowania. Pionowość instalacji wież linii napowietrznej 10 kV i poniżej oraz wsporników pojedynczych słupów 35 kV jest zwykle sprawdzana pionową linią. Poprawność montażu złożonych podpór - ich pionowość, prostopadła pozycja względem linii toru, położenie wsporników narożnych, a także wszystkie napowietrzne linie energetyczne powyżej 35 kV - sprawdzane są za pomocą przyrządów geodezyjnych (teodolit, poziom). Ponadto sprawdź poprawność montażu podpór na osi linii - montaż podpór w "celu" (na jednej linii prostej). Należy zachować następujące tolerancje:
odchylenie nośne od osi pionowej wzdłuż i wzdłuż osi linii (stosunek odchylenia górnego końca podpory do jej wysokości): jedno-drewniane 1/100, żelbetowe jedno-1/150, portalowe 1/100, metalowe-1/200 wysokości podpory;
wyjście podpory z wyrównania jednokolumnowych drewnianych i żelbetowych wsporników - 100 mm z rozpiętością do 200 mi 200 mm z rozpiętością ponad 200 m; wsporniki portalowe z betonu zbrojonego we wszystkich przypadkach - 200 mm; wsporniki metalowe o rozpiętości do 200 m - 100 mm, o rozpiętości od 200 do 300 m - 200 mm, powyżej 300 m - 300 mm.
Sprawdzona poprawka wsparcia w rowie lub na podstawie. Doły są pokryte warstwami ziemi o grubości 150-200 mm. Każda warstwa jest starannie ubita. Wsporniki żelbetowe z bliska w cylindrycznych rowach z zaprawą cementową po tymczasowym przymocowaniu ich klinami. Zaprawę cementową dostarczoną z mieszalni rozładowuje się na specjalną tacę zainstalowaną na podporze, a za pomocą kadzi i łopaty łopaty wypełniają zatoki wykopu. Zagęszczanie roztworu w zatokach wytworzonych przez splatanie metalowych prętów. Gdy temperatura powietrza wynosi + 10 ° C i więcej, kliny tymczasowe są usuwane po 24 godzinach, a przy średniej temperaturze dziennej wynoszącej + 5 ° C - po 48 godzinach "kieszenie" pozostawione po wykopaniu klinów są wypełnione ziemią, a gleba jest dodawana wokół podpory zgodnie z projekt.
(Dokument)
Ryc. 29. Instalacja wspornika drewnianego (żelbetowego) z pojedynczą zębatką dla linii napowietrznej 35-220 kV z dźwigiem:
a - układ
b - powstanie do obniżenia dołu;
1 - wysięgnik żurawia,
2 - wsparcie
3 - szybkie wydanie.
4 - rów.
Podobnie zainstalowane są pośrednie słupy w kształcie litery U z linii napowietrznych 35-110 kV o wadze do 2,5 tony.
Przy podnoszeniu wsporników żelbetowych 1-słupowych 1 za pomocą dźwigu instalacyjnego K-LEP-7 (rys. 30) są one układane wzdłuż osi VL, tak aby dolny koniec szafy znajdował się 1,5 m od środka wykopu 3. Dźwig 2 z podniesionym wysięgnikiem jest doprowadzany do wspornika od strony czołowej i zamontowane na wysięgnikach 4. Rozszerzony teleskopowy wysięgnik jest opuszczany na stojak i mocowany na nim w dwóch punktach. Następnie podnoszą wysięgnik razem ze wspornikiem w pozycji pionowej, opuszczają podporę do dołu, wyprostowują ją i wypełniają ziemią.
Ryc.30. Montaż wspornika żelbetowego jednobiegunowego dla linii wysokiego napięcia 35-220 kV z dźwigiem instalacyjnym K-LEP-7:
1 - wsparcie.
2 - dźwig
3 - rów
4 - wysięgniki podpory (podpory);
II i II - położenie podparcia podczas podnoszenia
Instalacjapojedynczy stojakżelbetowyobsługujeLinia napowietrzna35-220 kVdźwigiemiciągnik (Zdjęcie 31). Jeżeli niemożliwe jest zamontowanie podparcia za pomocą jednego dźwigu (na przykład w słabych glebach, gdzie wykop jest wykopany i dźwig nie może się zbliżyć), zmontowany wspornik 1 jest ułożony wzdłuż osi linii nad wykopanym wykopem 8, tak aby dolny koniec stojaka wynosił 1,5-2 m od strony dołu (pozycja /). Żuraw 4 jest zainstalowany w poprzek osi VL do wysięgników w odległości 0,5-1 m od środka ciężkości wspornika na krawędzi wykopu pod dolną podpórką poprzeczną. Dwa boczne szelki 3 kabla o długości około 50 m są zamocowane i umieszczone w dwóch wyciągarkach 2 zainstalowanych w odległości 25 -30 m od osi VL i od środka wykopu. Kabel hamulca 7, który dociera do wciągarki 6 ciągnika, jest przymocowany do słupka wsporczego, a drabina linowa jest używana do dolnego trawersu w celu usunięcia klamr po montażu.
Ryc. 31. Montaż wspornika żelbetowego z pojedynczym stelażem dla linii napowietrznej 35-220 kV z dźwigiem i ciągnikiem:
1 - wsparcie.
2 - wyciągarka.
3 boczne szelki.
4 - dotknij.
5, 7 - linki trakcyjne i hamulcowe.
6 - ciągnik,
8 - kute,
10 i 11 - położenie podparcia podczas podnoszenia
Najpierw podnośnik jest podnoszony przez żuraw na maksymalną możliwą wysokość (co najmniej 30-45 °), a dół zębatki, który jest hamowany przez wciągarkę ciągnika, opuszczany jest do studzienki. Gdy podpórka spoczywa na dnie wykopu (pozycja //), podnoszenie podparcia za pomocą dźwigu zostaje zatrzymane, kabel hamulcowy jest odłączony od ciągnika, a ciągnik zostaje przeniesiony na podporę. W tym celu kabel trakcyjny 5 jest przymocowany do wciągarki ciągnika i dokręcany, dopóki lina ładunkowa żurawia nie zostanie osłabiona. Następnie zawiesia dźwigowe zostają odłączone od podparcia, a dźwig przechodzi w tryb hamowania. W tym samym czasie boczne wyciągarki pociągają za szelki. Dalsze podnoszenie podparcia jest kontynuowane przez ciągnikową wciągarkę trakcyjną, regulując położenie podpory wzdłuż osi VL za pomocą bocznych szelek. Gdy zbliżamy się do pozycji pionowej, podpora jest hamowana przez te same wzmocnienia boczne. Po wyrównaniu podpory ustawiają śruby i zasypiają dół.
Podobnie zainstalowane są drewniane słupy w kształcie litery U linii napowietrznych 110 kV o wadze ponad 2,5 tony.
Czasami linka trakcyjna jest przymocowana nie do wciągarki, ale bezpośrednio do ciągnika i podnosić podporę, przesuwając ciągnik. W tym przypadku szczególną uwagę zwraca się na to, że ciągnik porusza się ściśle wzdłuż osi linii napowietrznej, a szelki są cały czas rozciągnięte. W wielu przypadkach szelki są przymocowane nie do wciągarek, ale do pojazdów silnikowych lub ciągników, co nieco upraszcza instalację wsparcia.
Wsporniki jednokolumnowe z aparatami ortodontycznymi są również instalowane za pomocą dźwigu i ciągnika. Przed podnoszeniem nogi podpór są połączone z fundamentami za pomocą zawiasów, wokół których podpora jest obracana podczas podnoszenia. W tym przypadku hamowanie dolnej części wsparcia nie jest wymagane. Przymocuj pręty na podporach, wykorzystując je jako boczne rozstępy. Po zamontowaniu podpory są mocowane do wcześniej zamontowanych płyt kotwiących i, regulując ich napięcie, prostują podpórkę.
Wsporniki narożne z klamrami są instalowane z lekkim nachyleniem do zewnętrznej strony kąta obrotu linii napowietrznej, tak aby później pod napięciem zamontowanych drutów zajmowały pozycję konstrukcyjną.
InstalacjaAP-
graficznydrewnianeobsługujeLinia napowietrzna35-220
kVspadastrzała(rys.32). Podczas instalowania tych podpór traktory T-100M są używane jako ciągniki, a spychacze służą jako kotwice.
Podpora 1 rozpościera się na podkładkach 13 wzdłuż osi wgłębień 12 tak, że osprzęt znajduje się powyżej wgłębień, pomiędzy którymi ustawia się strzałkę opadającą 7. Do wierzchołka bomu przymocować "wodze" 6. Wolne końce "wodze" są przymocowane do słupków podpory w miejscach ich połączenia z poprzeczką. Kabel trakcyjny 9 wciągarki 10 ciągnika jest zamocowany do górnej części bomu przez polstrum 8, dolne linki hamulcowe 2 są przymocowane do zamocowań w miejscach ich połączenia ze śrubami, a do środka trawersu - górny przewód hamulcowy 5. Tymczasowe rozpórki są instalowane w dolnej części kratownicy A i wzmacniają dodatkowe nakładki łączą konsole z regałami (jeśli są zrobione tyłem).
Ryc.32. Montaż drewnianej podpory w kształcie AP VL 35-220 kV z ciągnikami i opadającym wysięgnikiem:
1-wsparcie,
2.5 - dolny i górny przewód hamulcowy,
3,4 - ciągniki hamulcowe,
6 - "wodze",
7 - spadająca strzała,
8 - polyspast,
9- kabel trakcyjny
10 - wciągarka do ciągnika,
11 - ciągnik trakcyjny,
12 - rów, 1
13 - podszewka;
Pozycje I, II, III i I ', II', III 'podpory i strzałki w dół podczas podnoszenia
Na początku windy wspornik obraca się wokół wykładzin wokół punktów mocowania dolnych przewodów hamulcowych. Po obróceniu wspornika do 40-45 °, dolne linki hamulca zaczynają się łagodnie wypuszczać, a osprzęt opuszcza się całkowicie w dół do dna wgłębień. Dalsze podnoszenie odbywa się poprzez obracanie podpory wokół punktów zatrzymania przystawek w wykopach. Niższe linki hamulca zwalniają i przenoszą ciągnik na górny przewód hamulcowy.
Przy dalszym wznoszeniu spadająca strzałka gaśnie z pracy i zawiesza się na kablu trakcyjnym lub specjalnym sznurku, a podpora wysuwa się w pozycji pionowej i staje się czterema nasadkami. Następnie sprawdź jego położenie, doły zasypiaj i zdemontuj takielunek.
W ten sam sposób instalowane są ciężkie drewniane podpory pośrednie w kształcie litery U linii napowietrznych 220 kV.
InstalacjametalobsługujeLinia napowietrzna35-220
kV. Podpory metalowe są instalowane głównie tymi samymi metodami, co żelbet. Stojaki wolnostojące o pojedynczym stojaku o wadze do 4-5 ton i wysokości 10-15 metrów są unoszone za pomocą dźwigu ważącego 5-10 ton i. do 22 m wysokości - dźwigiem i ciągnikiem, ponad 10 ton - opadającym wysięgnikiem i ciągnikami. Podpory portalowe prawie wszystkich typów są instalowane ze spadającą strzałą i ciągnikami. Podpory pojedynczego słupka niektórych typów są podnoszone za pomocą dźwigów instalacyjnych KVL-8 lub KVL-12B.
Wspornik zainstalowany przez żuraw jest wstępnie ułożony na fundamencie, tak aby jego środek ciężkości był jak najbliżej środka fundamentu. Następnie podwieszany jest ponad środek ciężkości i podnoszony dźwigiem ponad fundamentem. Otwory w piętach podpory są wyrównane ze śrubami kotwiącymi, po czym stopniowo opuszczają podporę na fundament, sprawdzają i mocują śruby kotwiące.
Wsporniki, zainstalowane przez żuraw i traktor, są wcześniej układane ściśle wzdłuż osi trasy i mocowane w zawiasach na fundamentach, wzmocnione, jeśli to konieczne, drewnianymi rozpórkami. Zawiesie ładunku jest zamocowane powyżej środka ciężkości podpory, nad nią - do sztywnej przepony - kabel trakcyjny jest zaczepiony, a górna część podpory jest hamowana.
Podnoszą one podporę za pomocą dźwigu, obracając zawiasy o co najmniej 30-45 ° i ustawiając je w pozycji pionowej za pomocą ciągnika w taki sam sposób jak jednościenny żelbetowy. Następnie z każdą nogą podnoszą zawiasy, kładąc obcasy na śrubach kotwiących, sprawdzając i dokręcając nakrętki.
Instalacjaobsługujeprzez helikoptery. W trudnych warunkach, gdy konwencjonalne metody są niemożliwe lub ekonomicznie niepraktyczne, używaj śmigłowców. Wspornik montowany w miejscu instalacji jest dostarczany helikopterem do palety i natychmiast instalowany na przygotowanym fundamencie (metoda swobodnej instalacji podpór). Wstępne, specjalne urządzenia pułapkowe są instalowane na fundamentach, wyposażonych w demontowane pochyłe ścianki boczne. Zwykle ustawiony metal podtrzymuje stosunkowo małą masę.
Podpory metalowe są montowane helikopterem za pomocą zawiasów. Aby to zrobić, na dwóch fundamentach, wstępnie złożonych zawiasach o specjalnej konstrukcji, połącz z nimi obcasy (buty) wcześniej zmontowanej podpory i przymocuj kabel ładunkowy u góry. Helikopter, wznosząc się w powietrze, włącza wspornik kabla wokół zawiasów i wyświetla go w pozycji pionowej. Następnie wyjąć zawiasy i zamocować podparcie na fundamencie.
Podobnie, żelbetowe wsporniki portalowe i metalowe są czasami instalowane.
Wyrównanieimocowanieobsługuje. Podniesiona podpora musi być wyrównana, to znaczy musi być ustawiona w położeniu, w którym jej oś jest pionowa względem ziemi, a poprzeczki mają kąt 90 ° względem osi linii napowietrznej. Wszystkie podpory muszą znajdować się w wyrównaniu linii. Przekroje wsporników narożnych należy skierować wzdłuż dwusiecznej o kąt obrotu OHL.
Wsporniki wolnostojące są kalibrowane za pomocą tych samych dźwigów i mechanizmów trakcyjnych, które były używane podczas ich instalacji, i obsługują z wadami, pociągając za opóźnienie. Kontroluj wyrównanie teodolitu, pionu, lornetki. Pojedynczy stojak obsługuje wdrażanie w pozycji projektowej, różne urządzenia.
Po wyrównaniu podpory są ostatecznie zamocowane w gruncie lub na fundamentach. Podpory montowane bezpośrednio w ziemi są przymocowane, zasypiając pod ziemią, piaskiem, piaskiem i żwirem lub kruszywem (zgodnie z wytycznymi projektu). Podczas wypełniania warstw gleby ostrożnie baran.
Metalowe podpórki wolnostojące zabezpieczone nakrętkami na kotwach fundamentowych. Na wspornikach pośrednich jedna nakrętka jest zamontowana na śrubie, a dwie na śrubach kotwiących i narożnych. Wsporniki z mocowaniami są stałe, pociągając za opóźnienia, aby utworzyć w nich obliczony wysiłek, kontrolowany przez specjalne urządzenie.
Na zamontowanych podporach przymocuj cienką blachę stalową z numerem seryjnym i rokiem montażu podpory, a także plakaty ostrzegające przed niebezpieczeństwem. Podpory żelbetowe często są oznaczone pieczątkami.
Po wyrównaniu podpór, uziemienia są połączone z uziemionymi gniazdami lub śrubami uziemiającymi umieszczonymi w podstawie, które są ułożone podczas ich montażu. Na zbrojonym betonie i metalowe podpórki Takie połączenie wykonuje się za pomocą spawania lub zacisków śrubowych, a na połączeniach drewnianych - za pomocą zacisków śrubowych. W każdym przypadku powinno być dostępne połączenie uziemiających zboczy lub śrub z uziemieniem.
Instalacja podpór jest rejestrowana w dzienniku, w którym wprowadzane są odchylenia podpór i ich elementów od pozycji projektowej i innych danych.
Cechy konstrukcji podpór w trudnych warunkach
Budowa linii napowietrznych na obszarach o trudnych warunkach klimatycznych i trudnych warunkach geologicznych (na przykład na trasie linii brzegowej Bajkał-Amur) ma szereg cech, z których głównymi są niedostępność terenów budowlanych, brak zaplecza produkcyjnego i komunikacji komunikacyjnej, sezonowość poszczególnych prac, krótkie dni świetlne, trudność zamocowania podtrzymuje wieczną zmarzlinę i glebę osiadłą i marias (obszary bagienne, które nie zamrażają nawet w zimie), dużą stratę czasu pracy z powodu niskich temperatur (do -65 ° C), siły wiatry, deszcz, śnieg, itp. Szczególne trudności powstają podczas transportu materiałów i wyposażenia, montażu fundamentów, montażu i instalacji podpór.
Transport ładunków w obszarach niezabudowanych i trudno dostępnych realizowany jest głównie transportem multimodalnym, tzn. Wykorzystuje wszystkie możliwe środki transportu, w tym lotnictwo (śmigłowce), co prowadzi do wielokrotnego przeciążania, instalacji baz przeładunkowych i tymczasowych dróg, a także zwiększa koszt dostawy w dziesiątkach razy Jednocześnie, ze względu na brak i brak specjalnych urządzeń do transportu towarów w warunkach terenowych, konieczne jest stosowanie konwencjonalnych pojazdów produkcyjnych i mechanizmów, które są słabo dostosowane do trudnych warunków klimatycznych.
W północnej strefie klimatycznej większość towarów przewożonych jest drogami zimowymi - tymczasowymi drogami zimowymi, budowanymi według specjalnych zasad i wyposażonymi w punkty grzewcze, magazyny paliw i smarów oraz mieszkania.
Aby obniżyć koszty i poprawić niezawodność dostaw ładunku, opracowywane są nowe pojazdy specjalne i mechanizmy: poduszka powietrzna, aerostaty, sterowce, śmigłowce o wysokim udźwigu.
Budowa fundamentów w glebach wiecznej zmarzliny i na bagnach jest jednym z najważniejszych problemów w budowie linii napowietrznych. Jeżeli w normalnych warunkach koszt zamocowania wsparcia wynosi około 20-30% całkowitego kosztu jego budowy, na obszarach z wieczną zmarzliną i silnie zasypanymi glebami ich udział wzrasta do 60-70%. Dlatego najbardziej powszechnym w takich strefach są fundamenty różnych rodzajów, które znacznie zmniejszają lub całkowicie eliminują roboty ziemne.
Ponieważ fundamentów Svan na palach nie można wbijać w wieczną zmarzniętą ziemię, zanurza się je we wstępnie przygotowanych wgłębieniach prowadzących, dla których pożądana jest gleba do ogrzania. Tymczasem gleby wiecznej zmarzliny mają nośność tylko w stanie zamrożonym. Rozmrożona gleba jest upłynnioną masą. W związku z tym stosy zainstalowane w studniach mogą być ładowane dopiero po całkowitym zniszczeniu naruszonej i otaczającej ziemi, a stos w pojedynczy monolit.
Przenikanie dołków w glebach wiecznej zmarzliny w celu zanurzenia stosu odbywa się głównie na dwa sposoby: mechaniczne (wiercenie) i termiczne. W ostatnim czasie coraz powszechniejsze stają się metody łączone: szokowe, termomechaniczne i szokowo-obrotowe. Tak więc, za pomocą metody termomechanicznej, studnie są rozwijane za pomocą parowego wibro-lidera, w koronę o kształcie pierścienia tnącego, z której dostarczana jest para. Glebę ogrzewa się tylko nad pierścieniową sekcją korony. Po wniknięciu do odwiertu, zwierciny pozostają w ilości wystarczającej do wypełnienia przestrzeni między jej ścianami a stosem. Ta metoda poprawia wydajność i skraca czas zamrażania pali w ziemi.
Pale dla wiecznej zmarzliny są wykonane głównie z metalowych rur, a czasem z drewna i żelbetu. Najskuteczniejsze osłony termometryczne to wydrążony metalowy cylinder grubościennych rurek, którego wewnętrzne wgłębienie jest wypełnione amoniakiem lub innym czynnikiem chłodniczym (nafta, propan). Pogłębiają one termy, tak że ich dolny koniec znajduje się poniżej granicy sezonowego rozmrażania zmarzliny. W rezultacie gleba wokół palu ma latem ujemną temperaturę, a zatem nośność fundamentu jest stale utrzymywana.
W celu zainstalowania takich fundamentów wierci się je za pomocą instalacji MRK lub wibroizolatora parowego w gruncie studni o średnicy nieco większej od temperatury, zanurza w nim stos za pomocą dźwigu i wypełnia, jeśli to konieczne, przestrzeń między ścianą studni a palikiem z roztworem gleby (płuczka wiertnicza).
Ponadto, do budowy fundamentów palowych stosuje się stalowe wieloobrotowe słupy i kotwy śrubowe, które zanurzane są w ziemi za pomocą maszyn MRK, lub stosy drewniane, które są zakopywane przez stosunkowo lekkie mechanizmy.
Podczas budowy linii napowietrznej na bagnach unika się w jak największym stopniu obszarów o głębokich pokładach torfu, próbują one przechodzić przez bagno w linii prostej bez podpór narożnych, tam gdzie to możliwe, stosuje się fundamenty palowe, fundamenty pływające lub pływające. Svan jest zwykle zanurzany w torfie i wbijany w znajdującą się pod spodem warstwę gleby za pomocą kruszywa pchającego (na przykład SP-49) zamontowanego na ciągnikach marsjańskich T-100BMGP o szerokich torach.
Na glebach podmokłych, wiecznie zmarzniętych i falochronnych powstają fundamenty powierzchniowe, które są płaskimi, prostokątnymi ciężkimi ramami o znacznych rozmiarach swobodnie rozmieszczonych na powierzchni gruntu, które zwykle są składane z elementów żelbetowych, pali lub metalowych rur. Dla większej stabilności w piwnicy, komórki górnej żebrowanej powierzchni elementów żelbetowych są czasami wypełnione glebą. Duża masa takich fundamentów i odpowiednio znaczna wytrzymałość powierzchni gruntu na ścinanie są przeciwdziałać zewnętrznymi obciążeniami wywracającymi. Fundamenty nawierzchniowe wsporników pośrednich można zestawić z czterech stosów żelbetowych: dwa układa się na wyrównanej powierzchni gleby na osi linii napowietrznej pod piętami podpór, a dwie, które działają jak przeciwwagi, znajdują się wzdłuż osi linii napowietrznej wzdłuż krawędzi ułożonych pali. Podstawy podpór pod kątem kotwicy są składane z dziesięciu palików złożonych we wspólną strukturę za pomocą stalowych zacisków, kątowników i uszczelek.
Fundamenty powierzchni metalowych (ryc. 33) są prostokątną ramą rozciągniętą na osi VL od rur 1, do której przyspawane są stopki wsporcze 2. Czasami końce rur są wygięte do góry, co pozwala na przeniesienie fundamentu do miejsca instalacji za pomocą włókna.
Ryc.33. Fundament powierzchni metalowych rur:
1 - rury.
2 pięty,
3 - spoina spawalnicza
Do montażu podpór na bagnach otwartych, gdzie niemożliwe jest zamontowanie fundamentów nawierzchni, zastosowano pływające fundamenty wykonane z cylindrycznych metalowych pływaków połączonych mostami z rur.
Montaż i instalacja podpór odbywa się w sposób, który wymaga minimalnej siły roboczej na autostradzie. Podpory żelbetowe są najmniej pracochłonne, jednak niewystarczająca mrozoodporność betonu i trudność transportowania regałów nie pozwalają na ich wykorzystanie. Dlatego specjalne stalowe i drewniane podpory o zredukowanej masie, zaprojektowane do pracy w temperaturze -40 ° C, są dość proste w montażu i instalacji. Stojaki takich stalowych słupów linii napowietrznych 110 kV i niewielkich odcinków pośrednich jednobiegunowych słupów linii napowietrznych 220 kV są gromadzone na wysypiskach i transportowane na trasę dowolnymi środkami, w tym helikopterami. Do zasilania pól gazowych i naftowych w strefie północnej stosuje się lekkie wsparcie linii napowietrznych 35-110 kV wykonanych z rur metalowych.
Konstrukcja z lekkiego połączenia śrubowego podpora stalowa VL 110 kV, w połączeniu z fundamentem, którego rolą zajmują się metalowe zbiorniki, zamontowane w dolnej części podstawy. Ciężar nośnika wraz z fundamentem wynosi 3 t. Podparcie jest dostarczane do miejsca instalacji, zmontowane, zainstalowane na wyrównanej powierzchni gruntu, a zbiorniki są napełniane statecznikiem, po czym uzyskuje on niezbędną stabilność i jest gotowy do zainstalowania przewodów.
Drewniane podpory o uproszczonej konstrukcji są instalowane na palach, zamarznięte w wiecznej zmarzlinie. Tak więc, kratownice w kształcie litery A z linii napowietrznych 6-10 kV (ryc. 34) są montowane z części fabrycznych, na składowisku lub autostradzie i instalowane na drewnianych palach 3 za pomocą zawiasów 2.
Ryc.34. Instalacja Wspornik w kształcie litery A dla linii napowietrznych 6-10 kV na drewnianych palach w wiecznej zmarzlinie:
1 - wsparcie.
2 - zawias,
3 - drewniany łabędź,
4 - ława żaroodporna,
5 - granica między warstwami gleby czynnej i wiecznej
3. OCHRONA ŚRODOWISKA I INSTRUKCJE BEZPIECZEŃSTWA
Ochrona środowiska
Budowa linii napowietrznej, jak każda inna działalność produkcyjna człowieka, jest szkodliwa dla środowiska. Znajduje to odzwierciedlenie w uszkodzeniu górnej żyznej warstwy ziemi, wycinaniu drzew i krzewów, cięciu upraw, naruszaniu stabilności powierzchniowej warstwy gleby w półpustyniach i wiecznej zmarzlinie w strefie tundry i lasu-tundry, a także śmierci ptaków, szkodliwym działaniu silnych pól elektromagnetycznych na zdrowie ludzi i zwierząt oraz inne
Najbardziej znaczące szkody w naturze wynikają z alienacji w ramach VL gruntów ornych (wyłączając je z płodozmianu). Dlatego z reguły w przypadku budowy linii napowietrznych ziemia nie nadaje się do rolnictwa. W wyjątkowych przypadkach linie napowietrzne są kładzione przez pola, a ich trasa jest zwykle położona wzdłuż dróg, wąwozów, pasów leśnych i innych oznaczników. Jednocześnie szerokość pasa gruntowego w niezamieszkanych obszarach przeznaczonych na okres budowy OHL wynosi nie więcej niż 8-17 m, a powierzchnia dodatkowych działek w miejscach montażu i instalacji podpór wynosi nie więcej niż 150-800 m (dla VL 1-220 kV). W obszarach zaludnionych wymiary te wynikają z projektu.
W obszarach przydziału linii napowietrznych należy podjąć środki w celu zachowania żyzności terenu. Podczas kopania rowów i rowów górna warstwa gleby powinna zostać przecięta i wepchnięta na hałdy przed rozpoczęciem pracy, a po zakończeniu prac należy ją założyć (rekultywacja terenu). Uszkodzenie żyznej warstwy można zmniejszyć, stosując maszyny i mechanizmy o niskim nacisku na podłoże, a także wykonując pracę w okresie zimowym. Właściwy czas budowy linii wysokiego napięcia (na przykład po zbiorach) pozwala uniknąć uszkodzenia upraw.
Szczególną uwagę należy zwrócić na ochronę środowiska podczas pracy w strefie wiecznej zmarzliny. Niszczenie roślinności, która zatrzymuje wilgoć i pokrywa ziemię przed bezpośrednim działaniem promieni słonecznych, łamie stabilność powierzchniowej warstwy ziemi, zwiększa głębokość sezonowego zamrażania i rozmrażania gleby, aw rezultacie prowadzi do wybrzuszenia (pchnięcia) fundamentów i podpór. W tym przypadku znaczące falowanie gleby, tj. wzrost jego objętości podczas zamrażania następuje zwykle na głębokości 2 m. Jeszcze większe zakłócenia równowagi naturalnej występują podczas termicznej metody wiercenia otworów na palach. Dlatego przede wszystkim konieczne jest zorganizowanie transportu ładunków ściśle wzdłuż dróg, ponieważ gleby zamarznięte i bagienne nieodwracalnie deformują się wraz z intensywnym ruchem pojazdów gąsienicowych oraz ograniczają termiczne metody wydobywania.
Podczas transportu materiałów wzdłuż autostrady niemożliwe jest rozbicie krzaków i drzew, uszkodzenie powierzchniowej warstwy ziemi i zanieczyszczenie gleby produktami maszyn i mechanizmów. Aby wyeliminować osunięcia się ziemi na zboczach, konieczne jest użycie pochyłych podpór o różnych długościach podpór i opóźnień, co pozwala porzucić poziomowanie gleby w miejscu montażu podpór. Zmniejszenie szerokości polan w pobliżu podpór znacznie zmniejsza ścinanie drzew. Takie polany mogą być zakrzywione lub schodkowe. Aby uratować ptaki, siadają na drutach i przekręcają gniazda w miejscach ich mocowania na podporach, specjalnie układają ogrodzenia, okonie, gniazda w bezpiecznych miejscach.
Szkodliwe oddziaływanie silnych pól elektromagnetycznych linii wysokiego i bardzo wysokiego napięcia jest zmniejszane przez umieszczenie ich przewodów na takiej wysokości, że pole elektryczne nie przekracza dopuszczalnych wartości (odpowiednio 15 i 5 kV / m, w niezamieszkałych i zaludnionych obszarach, 10 kV / m - na skrzyżowaniach dróg). Dlatego też ultra wysokie napięcie VL, z reguły, wznosi się nie bliżej niż 250-300 m od granic osiedli.
Aby zachować otaczające krajobrazy podczas budowy napowietrznej linii przesyłowej, konieczne jest poprawienie wyglądu podpór z estetycznego punktu widzenia, a także zlokalizowanie ich na autostradzie tak, aby wyróżniały się one jak najmniej na terenie i harmonizowały z nim.
Bardzo duże szkody w środowisku spowodowane są pożarami, zwykle występującymi w okresie wiosenno-letnim. Dlatego przy budowie linii wysokiego napięcia należy zwrócić szczególną uwagę na środki zapobiegania pożarom. Konieczne jest, aby prześwity OHL w trakcie budowy zostały oczyszczone z suchych zwalonych drzew, chrustu, krzewów i innych palnych materiałów, kominki powinny zostać wykopane, a nie usunięte stosy drewna i resztek drewna powinny być ograniczone do zmineralizowanych pasów o szerokości 1 m ziemia). W osiedlach mieszkalnych, na terenach magazynów i parkingów maszyn i mechanizmów konieczne jest posiadanie kompletnych zestawów środków gaśniczych (gaśnice, pompy, haki, wiadra itp.).
Po zakończeniu robót budowlanych i instalacyjnych, powierzchnia konstrukcyjna napowietrznej linii przesyłowej musi zostać doprowadzona do stanu odpowiedniego do użycia zgodnie z przeznaczeniem.
Podstawowe postanowienia ochrony pracy
Ochrona zdrowia pracowników, zapewnienie bezpiecznych warunków pracy, zapobieganie chorobom zawodowym i urazom przemysłowym to główne problemy rosyjskiego państwa. Każdego roku wydawane są miliony rubli na środki ochrony pracy. Szczególną uwagę zwraca się na ochronę pracy przy produkcji robót w warunkach innych niż normalne.
Zasady i przepisy bezpieczeństwa dotyczące budowy linii napowietrznych podano w Rozdz. "Bezpieczeństwo w budownictwie" Kody i przepisy budowlane, a także w Standardy państwowezawarte w Systemie standardów bezpieczeństwa (SSBT) i mają zastosowanie do wszystkich organizacji budowlanych i instalacyjnych.
Według SNiP odpowiedzialność za wdrażanie norm i przepisów bezpieczeństwa w organizacjach budowlanych i instalacyjnych spoczywa na głównych inżynierach i przełożonych, którzy muszą planować środki ochrony pracy, przeprowadzać terminowe szkolenia i instrukcje dla pracowników i inżynierów oraz badać każdy wypadek produkcyjny.
Wdrożenie środków bezpieczeństwa i higieny przemysłowej w miejscu pracy, poinstruowanie pracowników o bezpieczeństwie w miejscu pracy i terminowe szkolenie w zakresie bezpiecznych praktyk pracy są przydzielane do brygadzistów i rzemieślników. Nadzór nad stanem technicznym mechanizmów, maszyn, narzędzi i urządzeń, terminowe testowanie i instruktaż obsługujących je pracowników spoczywa na mechanikach i głównej mechanice organizacji budowlano-montażowych.
We wszystkich organizacjach budowlanych i instalacyjnych powinna zostać utworzona usługa inżynierii bezpieczeństwa, kierowana przez głównego inżyniera, którego pracownicy mogą zabronić pracy na terenie w przypadku naruszenia zasad bezpieczeństwa i wymagają od kierowników budowy wykonywania ściśle zgodnych z SNiP i zasad bezpieczeństwa.
Nowo przybyli pracownicy mogą pracować wyłącznie po wstępnym (ogólnym) instruktażu na temat bezpieczeństwa i higieny przemysłowej oraz podstawowej informacji na temat bezpieczeństwa bezpośrednio w miejscu pracy. Ponadto w ciągu jednego miesiąca nowo przybyli pracownicy powinni zostać przeszkoleni w zakresie bezpiecznych praktyk pracy i procedur udzielania pierwszej pomocy ofiarom prąd elektryczny i inne wypadki i zdać odpowiednie egzaminy. Badanie wiedzy jest przeprowadzane przez komisję pod przewodnictwem głównego mechanika i jest zapisane w protokole. W trakcie dalszych prac, ponowna odprawa w miejscu pracy powinna być przeprowadzana systematycznie, co najmniej raz na trzy miesiące i przy każdym przeniesieniu do innej pracy. Instrukcję zapisuje się w specjalnym dzienniku.
Pracownicy wykonujący roboty budowlano-montażowe o podwyższonych wymaganiach bezpieczeństwa (wspinanie, załadunek i rozładunek) muszą być przeszkoleni w ramach specjalnych programów i posiadać zaświadczenia o prawie do wykonywania tych prac. Personel obsługujący maszyny, urządzenia, instalacje i instalacje kontrolowane przez Gosgortechnadzor Federacji Rosyjskiej musi być przeszkolony i posiadać certyfikaty podpisane przez inspektora Gosgortekhnadzor.
Inżynierowie elektryczni obsługujący instalacje elektryczne, zgodnie z zasadami Państwowej Federalnej Służby Nadzoru Federacji Rosyjskiej, po szkoleniu i testowaniu, przypisują grupom kwalifikacyjnym środki bezpieczeństwa od pierwszej do piątej, w zależności od poziomu wiedzy i stażu pracy. Pracownicy wykonujący pracę o podwyższonych wymaganiach dotyczących bezpieczeństwa (wspinacze, elektrycy) muszą przejść wstępne i okresowe (raz w roku) badania lekarskie.
Osoby, które nie ukończyły 18 lat, które przeszły badanie lekarskie, mają doświadczenie w pracach wspinaczkowych co najmniej jednego roku i nie niższym niż trzeci poziom taryf, mogą samodzielnie wykonywać prace wspinaczkowe. Po raz pierwszy pracownicy zatrudnieni przy wspinaniu muszą pracować pod bezpośrednim nadzorem doświadczonych elektryków wyznaczonych przez kierownika organizacji na okres jednego roku. Wspinaczka to wszystkie prace wykonywane na wysokości większej niż 5 m od powierzchni ziemi, podłogi lub pokładu roboczego. Uczniom szkół zawodowych i szkół technicznych w wieku od 17 do 18 lat można się wspinać nie dłużej niż trzy godziny dziennie na szkolenie praktyczne (kształcenie zawodowe) pod stałym przewodnictwem i nadzorem mistrza szkolenia zawodowego i pracownika wyznaczonego na podstawie polecenia nadzorowania praktyka.
Liniowy personel inżynieryjny (brygadziści, brygadziści, mechanicy) musi przejść coroczny test znajomości przepisów bezpieczeństwa. Pracownicy inżynieryjni i techniczni obsługujący obiekty kontrolowane przez Gosgortekhnadzor muszą ponadto co najmniej raz na trzy lata zdawać egzaminy zgodnie z odpowiednimi przepisami.
Kontrola nad wdrażaniem przepisów bezpieczeństwa w trakcie pracy jest powierzona inspektorom technicznym regionalnych organizacji związkowych i publicznych inspektorów bezpieczeństwa wybranych przez lokalne organizacje związkowe.
Kierownicy, inżynierowie i technicy są administracyjnie i karnie odpowiedzialni za niedopełnienie obowiązków związanych z przestrzeganiem przepisów bezpieczeństwa i higieny przemysłowej.